螺桿空壓機品牌主機技術(shù)解析
作者:admin 發(fā)布日期:2019-10-30 10:28:56 關(guān)注次數(shù):
次瀏覽
二維碼分享
主機裝配排氣間隙:0.04~0.08mm,不超過0.15mm;主機軸承間隙一定小于排氣間隙(0.00~0.25<0.04~0.08);陰陽轉(zhuǎn)子分開時吸氣,合攏時排氣,主機上的定位銷是為保證裝配時轉(zhuǎn)子與進氣軸承座及機殼的同心度。
主機可用PTFE骨架油封,但應(yīng)注意軸的旋轉(zhuǎn)方向,油封上標L為左旋R為右旋,電機與壓縮機直聯(lián)選L,電機與壓縮機有增速齒輪的選R;電機方向一定要符合壓縮機箭頭所示方向,壓縮機上箭頭所示的旋轉(zhuǎn)方向是由生產(chǎn)單在設(shè)計時決定的,如電機帶其反向旋轉(zhuǎn)將造成主機轉(zhuǎn)子受力方向不對。
空氣濾芯前后壓差0.005Mpa,壓差過大會增加電機功率同時減少產(chǎn)氣量油分濾芯前后壓差0.1Mpa,壓差過大會增加電機功率同時減少產(chǎn)氣量油過濾器前后壓差0.2Mpa,壓差過大會造成排氣溫度過高;螺桿式空壓機內(nèi)潤滑油主要作用是冷卻、密封、潤滑,其必須選擇防氧化、防泡沫、防乳化、防銹蝕的專用潤滑油,建議使用空壓機專用油,而影響潤滑油的使用壽命主要在于環(huán)境差、長期高溫運行、排氣溫度過低或使用不同牌號的油時換油不徹底、混油造成;螺桿式空壓機分為風(fēng)冷型機組和水冷型機組,應(yīng)根據(jù)使用環(huán)境給予選擇。
通常螺桿機都有兩套壓力調(diào)節(jié)系統(tǒng),分別為通斷調(diào)節(jié)及穩(wěn)壓(無級)調(diào)節(jié),其螺桿式空壓機主要保護功能;主電機過載、風(fēng)扇電機過載、排氣溫度過高,水流量過壓、熱電耦斷線等:螺桿式空氣壓縮機的啟動方式:Y△啟動、自藕降壓啟動,目的都在于減小啟動時的電流,降低對電網(wǎng)的沖出
主電機過載的原因:電網(wǎng)電壓過低、外接電源線選型錯誤或接線端子松動,接觸器接觸不良、排氣壓力過高、空濾及油分濾芯堵塞、熱保護開關(guān)故障、主電機故障、主機頭故障風(fēng)扇電機過載的原因:冷卻器表面堵塞、風(fēng)扇電機故障,熱保護開關(guān)故障。
排氣溫度過高的原因:
1、無潤滑油或油位過低、油過濾器堵塞、環(huán)境溫度過高、斷油閥卡死、冷卻器堵塞,溫控閥失靈、溫度表失靈、潤滑油結(jié)焦或主機軸承間過大。
2、空壓機不加載的原因:氣管路上壓力額定負荷壓力壓力調(diào)節(jié)器斷開、電磁閥失靈、進氣閥故障、電磁閥到進氣閥的控制管路有泄漏。
3、加/卸載頻繁的原因:用戶管網(wǎng)系統(tǒng)有泄漏、加/卸載壓力設(shè)定錯誤、空氣消耗量不穩(wěn)定或未配小配儲氣罐、機組供氣管路中裝設(shè)有止回閥,而控制氣取壓點未移至止回閥后。
主機可用PTFE骨架油封,但應(yīng)注意軸的旋轉(zhuǎn)方向,油封上標L為左旋R為右旋,電機與壓縮機直聯(lián)選L,電機與壓縮機有增速齒輪的選R;電機方向一定要符合壓縮機箭頭所示方向,壓縮機上箭頭所示的旋轉(zhuǎn)方向是由生產(chǎn)單在設(shè)計時決定的,如電機帶其反向旋轉(zhuǎn)將造成主機轉(zhuǎn)子受力方向不對。
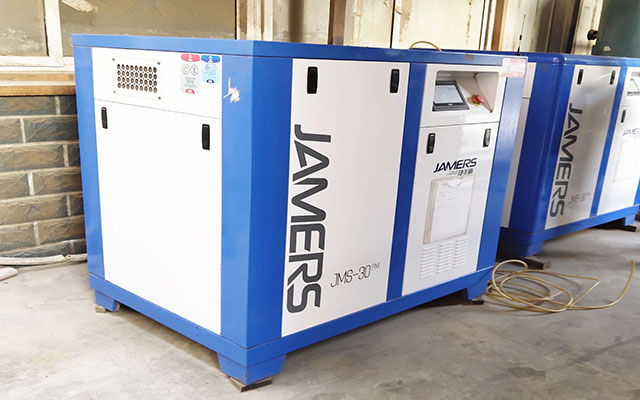
通常螺桿機都有兩套壓力調(diào)節(jié)系統(tǒng),分別為通斷調(diào)節(jié)及穩(wěn)壓(無級)調(diào)節(jié),其螺桿式空壓機主要保護功能;主電機過載、風(fēng)扇電機過載、排氣溫度過高,水流量過壓、熱電耦斷線等:螺桿式空氣壓縮機的啟動方式:Y△啟動、自藕降壓啟動,目的都在于減小啟動時的電流,降低對電網(wǎng)的沖出
主電機過載的原因:電網(wǎng)電壓過低、外接電源線選型錯誤或接線端子松動,接觸器接觸不良、排氣壓力過高、空濾及油分濾芯堵塞、熱保護開關(guān)故障、主電機故障、主機頭故障風(fēng)扇電機過載的原因:冷卻器表面堵塞、風(fēng)扇電機故障,熱保護開關(guān)故障。
排氣溫度過高的原因:
1、無潤滑油或油位過低、油過濾器堵塞、環(huán)境溫度過高、斷油閥卡死、冷卻器堵塞,溫控閥失靈、溫度表失靈、潤滑油結(jié)焦或主機軸承間過大。
2、空壓機不加載的原因:氣管路上壓力額定負荷壓力壓力調(diào)節(jié)器斷開、電磁閥失靈、進氣閥故障、電磁閥到進氣閥的控制管路有泄漏。
3、加/卸載頻繁的原因:用戶管網(wǎng)系統(tǒng)有泄漏、加/卸載壓力設(shè)定錯誤、空氣消耗量不穩(wěn)定或未配小配儲氣罐、機組供氣管路中裝設(shè)有止回閥,而控制氣取壓點未移至止回閥后。